Customer name: An ultrasound company
Equipment model: CW6163X2000 large ordinary lathe
Application site: transformation of large ordinary lathe
Installation position: the back of the knife holder
Product model: P100-032410
The CW6163X2000 large-scale ordinary lathe has 12 lubrication points, which lubricate the screw rod and the rotating tool post respectively, and the lathe operator is responsible for maintenance. The main shaft, screw rod, slide block, and slide block of the lathe are regularly maintained once every three days, which requires a lot of maintenance. Since maintenance is performed by operators who operate the lathe, manual maintenance is performed manually, and the quality of maintenance and the time of maintenance cannot be guaranteed, which will affect the stability of the equipment.
This time, we recommend the installation of a single-line centralized lubrication system based on the distribution of lubrication points of the equipment. The main components of the system include: P100-032410 300ml compact pressure relief electric grease pump, 1 pressurized distributor, 12 outlets, high pressure grease resin hose 5 meters, mainly used for the main line, and There are several pipe fittings and so on.
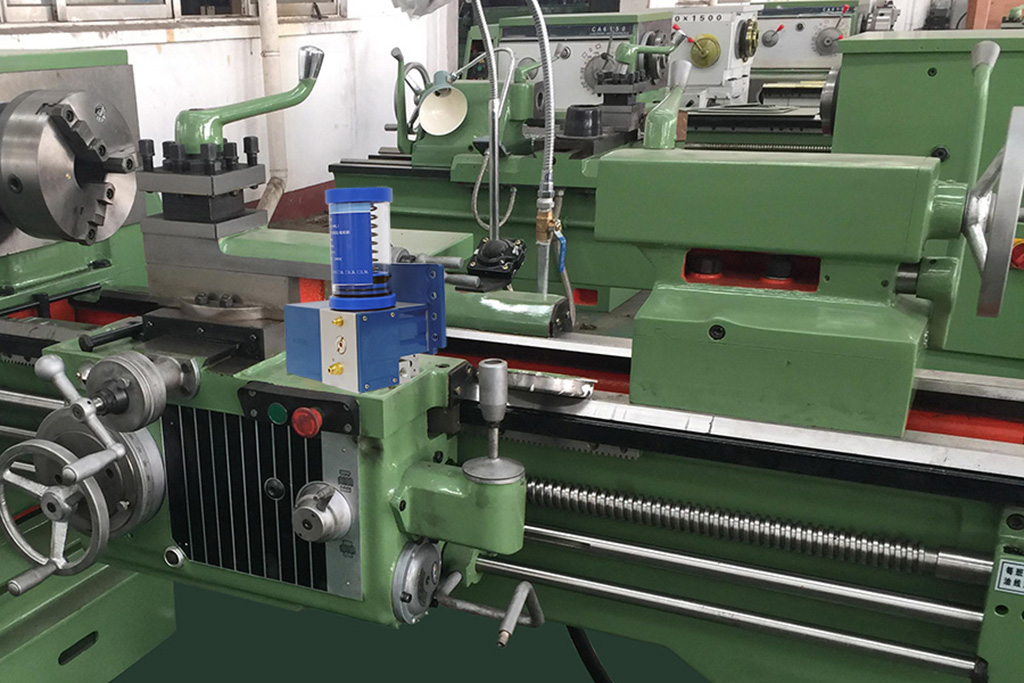
The installation of the centralized lubrication system must adopt a flatter and space-saving way. The location of the pump installation will not affect the operation of the lathe, so we install the pump on the side part, which is easy to operate and safe. Since the lathe only needs to be lubricated once every three days, we try to set the system to the machine start time to control the operation of the pump.
The centralized lubrication system developed by our company is designed according to the amount of grease required for reasonable lubrication of mechanical equipment under operating conditions, and realizes that the lubrication cycle can be set according to the use time of the equipment during operation. The system can automatically and force lubrication regularly and quantitatively to ensure that the equipment is effectively lubricated, reduce friction loss, reduce operating costs, improve operating efficiency, extend component life, and improve equipment safety.