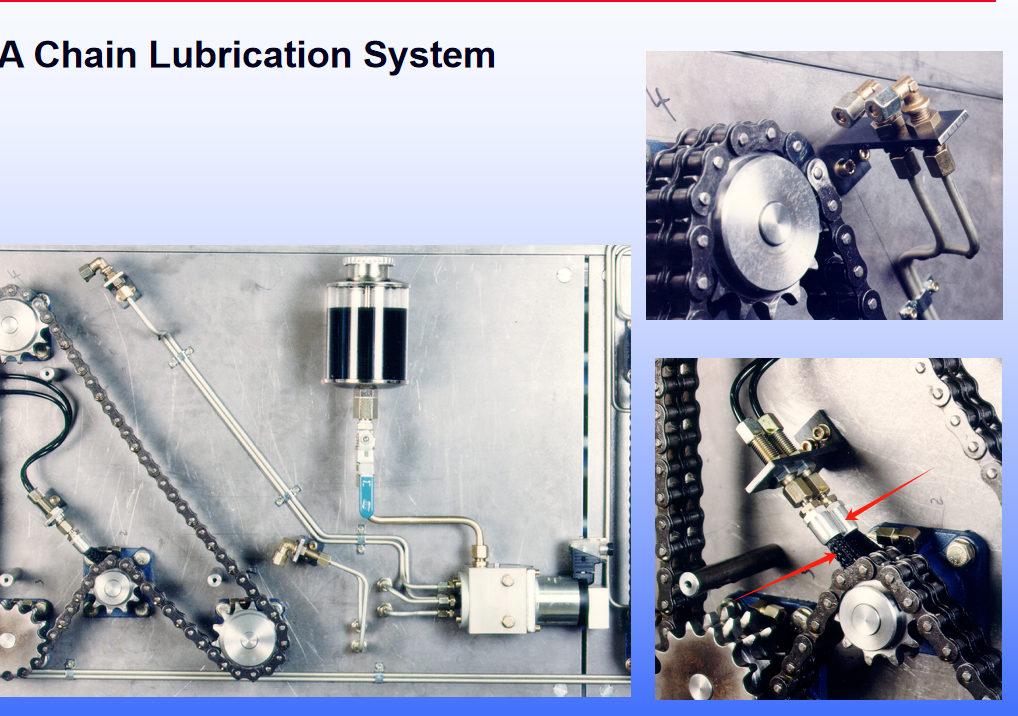
Designing an automatic lubrication system for chains is essential to ensure smooth operation, minimize wear, and extend the lifespan of chain-driven machinery. Let’s explore the key considerations and steps involved in creating an effective chain lubrication system:
1. Importance of Chain Lubrication
Chains play a critical role in various industrial processes, such as conveyor systems, manufacturing lines, and agricultural machinery. Proper lubrication is vital to prevent premature wear, reduce friction, and maintain optimal performance. An automatic lubrication system offers several advantages over manual lubrication:
- Maximize Chain Service Life: Consistent lubrication helps prolong chain life.
- Minimize Downtime: Adequate lubrication reduces the risk of unexpected breakdowns.
- Optimize Lubricant Consumption: Precise delivery ensures efficient use of lubricants.
- Enhance Worker Safety: Automated systems reduce manual handling of lubricants.
- Reduce Labor Time: Automatic lubrication eliminates the need for frequent manual checks.
2. System Design Steps
When designing an automatic chain lubrication system, consider the following steps:
2.1. Grease Selection
Choose a high-quality grease suitable for chain applications. Factors to consider include temperature range, load capacity, and compatibility with chain materials.
2.2. Identify Lubrication Points
Identify critical lubrication points along the chain. These typically include roller bearings, pins, and bushings. Proper lubrication at these points prevents excessive wear and reduces noise.
2.3. Select the Lubrication Method
Several lubrication methods are available:
- Air-Assisted Oil Projection System: Ideal for fast-moving conveyor roller chains, this system delivers a thin layer of oil without direct chain contact. It ensures precise lubrication at preset intervals 1.
- Airless Oil Projection System: Designed for large, slow-moving chains, this system meters oil directly onto the chain surface at specific link locations. It operates without chain contact, ensuring consistent lubrication 1.
- Oil Applicators: These work well with small, fast-moving chains. Oil applicators, integrated with automatic lubrication systems, provide controlled lubrication 1.
- Grease Injection System: Specifically for chains requiring grease lubrication, this system delivers metered amounts of lubricant to each link while the chain is in motion. Models like COBRA and GVP follow this principle 1.
2.4. Waste Oil Recovery
Address waste oil management. Consider vacuum-based recovery or suction and drainer devices to remove excess grease and prevent contamination 1.
3. Environmental Impact
Efficient chain lubrication not only benefits machinery but also contributes to environmental protection by reducing waste oil pollution. Properly designed systems enhance equipment reliability and support sustainable industrial processes 1.
In conclusion, an automatic chain lubrication system ensures smoother operations, reduces maintenance efforts, and promotes a greener future. By implementing the right design and maintenance practices, we can keep our chains running smoothly and efficiently.