Selecting the right lubrication system for an excavator is crucial for optimal performance and longevity. Let’s delve into the essential aspects of lubricants and their application, ensuring peak efficiency and durability for your excavators:
lubrication system
- Understanding the Functions of Lubricants:
- Reducing Friction and Wear: Lubricants create a protective layer between moving parts, minimizing wear and tear. This enhances efficiency and reduces maintenance requirements.
- Protection Against Corrosion: Harsh environmental conditions can lead to metal corrosion. Lubricants act as a barrier, preventing direct contact with moisture and chemicals.
- Controlling Contamination: Formulated to resist dust and dirt ingress, lubricants keep internal components clean, maintaining machinery efficiency.
- Temperature Management: Lubricants dissipate heat from moving parts, preventing overheating and associated damage.
- Types of Lubrication Systems:
- Automatic Progressive Lubrication System: This system gradually delivers lubricant to various points in the excavator. It uses progressive divider blocks to distribute grease or oil. These systems are reliable and suitable for heavy machinery like excavators.
- Centralized Automatic Lubrication System: A centralized system delivers lubricant to multiple points simultaneously. It ensures consistent lubrication and reduces manual effort.
- Factors to Consider:
- Application: Consider the excavator’s specific requirements, such as load, operating conditions, and environmental factors.
- Cost: Evaluate the initial investment, maintenance costs, and long-term savings.
- Real-World Applications: Learn from case studies and industry experts to understand practical benefits.
- Consult Experts:
- Reach out to lubrication system providers or consult with maintenance professionals to tailor the system to your excavator’s needs.
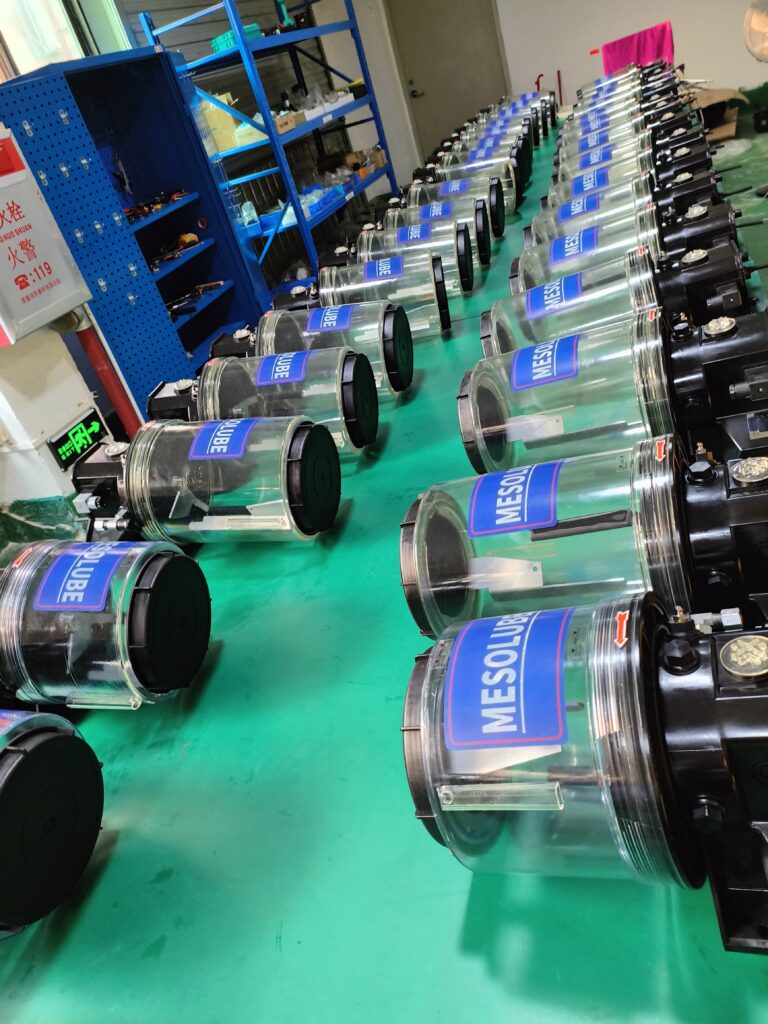